O fluxo de materiais no armazém responde a uma das suas características intrínsecas, uma vez que a permanência dos produtos dentro do armazém é temporária e tudo que entra na instalação deverá sair. O fluxo no armazém pode ser simples ou complexo, dependendo de cada empresa, das operações internas que são efetuadas com a mercadoria, da quantidade da mesma e da forma de fazer a sua movimentação. Os diferentes fluxos de materiais podem ser ilustrados por simples fluxogramas ou diagramas de fluxo.
Os tipos de fluxo de materiais no armazém
Os fluxos de materiais são as movimentações realizadas com as unidades quando entram no armazém, dentro do armazém e ao saírem.
- Fluxo simples: para entender como são feitas essas movimentações, podemos exemplificar a começar com o fluxo mais simples, aquele que ocorre quando são fornecidas, sem fracionar, as mesmas unidades de carga enviadas pelo fornecedor.
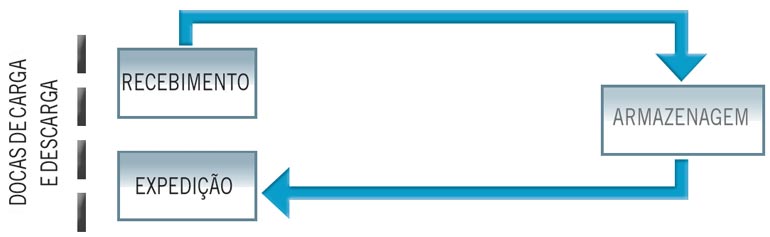
Fluxo simples de materiais num armazém
- Fluxo médio: neste tipo de fluxo, as movimentações começam a ficar mais complexas. É o que costuma ocorrer em armazéns com operações simples de picking ou combinadas, geralmente, com o fornecimento de paletes completas.
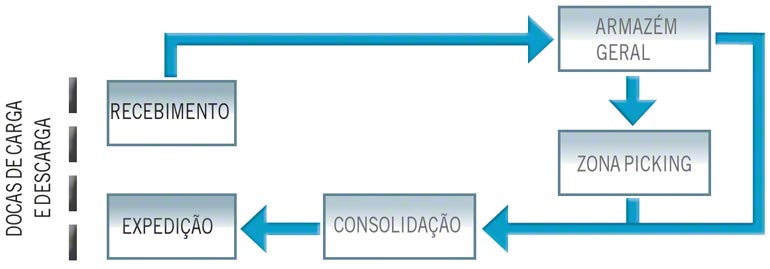
Fluxo médio de materiais num armazém
- Fluxo complexo: há armazéns que contam com diferentes zonas de trabalho dependendo dos tipos de produto e do seu consumo. Costumam dispor de zonas de manipulação intermédias e podem precisar de diversas operações que exijam fluxos com uma certa complexidade e, por vezes, de grande complexidade. Mediante o diagrama a seguir podemos observar um exemplo desse tipo de instalação e as movimentações de cargas que podem ocorrer dentro dela.
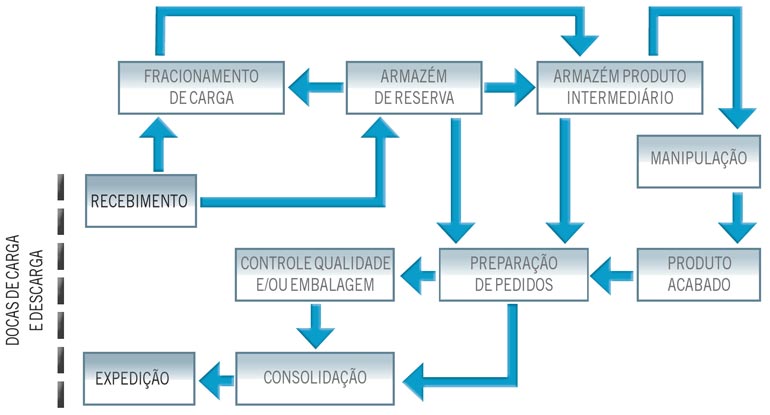
Diagrama de fluxo complexo de materiais no armazém
Verifica-se que cada fluxo de materiais no armazém adicionado ao sistema de trabalho representa um custo extra, somado ao custo total do processo efetuado dentro do armazém. Quanto maior o fracionamento a ser realizado relativamente às unidades de carga, maior será o impacto no custo. As operações de picking são as que têm um maior peso – podem superar os 60% – no montante total das operações do armazém. Por isso, o layout dessas zonas é muito importante.
Por outro lado, quanto maior for o armazém, maior será o percurso a ser efetuado pelos equipamentos de movimentação e pelos funcionários, consequentemente, o custo final da operação será mais alto. Em centros com muita movimentação, é necessário analisar a conveniência de recorrer à automatização para que o produto vá até ao homem no lugar de o homem ir até ao produto.
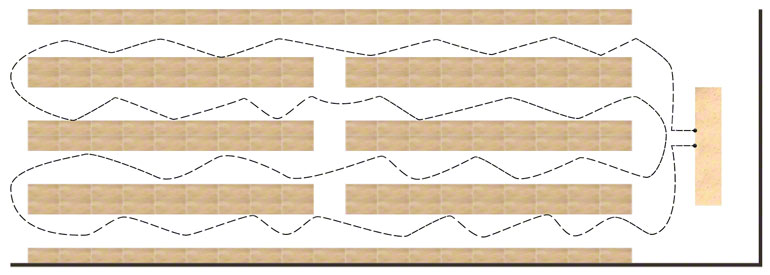
Armazém de picking com operação do homem ao produto
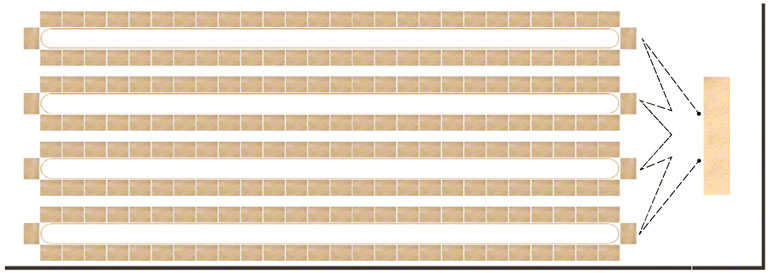
Armazém de picking com operação do produto ao homem
Podemos deduzir que também é fundamental a localização das referências de acordo com o seu consumo ou o seu volume. Quanto mais perto os cais de carga e descarga estiverem das mercadorias que têm uma maior procura ou maior tamanho, menor será o custo de manipulação.
Um bom exemplo pode ser um armazém onde as unidades soltas são preparadas diretamente. Uma só palete pode conter centenas de unidades de venda, portanto, ao movimentá-la com uma só operação é possível evitar centenas de movimentações que deveriam ocorrer ao preparar cada uma dessas referências soltas.
Todas as operações exigem que uma pessoa, um equipamento (ou ambos), possam executá-las. Por isso, é fundamental conseguir que um mesmo operário efetue o maior número de ações num determinado período de tempo, ou em outros termos, utilizar em cada operação o menor tempo possível. Isso pode ser aplicado em todas as atividades do armazém, embora esse princípio seja especialmente importante no que se refere ao picking, uma vez que é a atividade que mais prevê movimentações.
A rotatividade dos produtos A-B-C
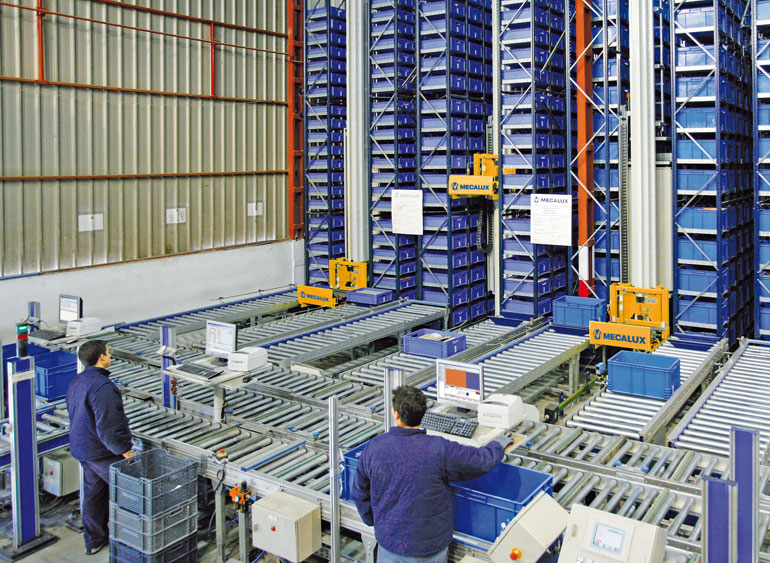
Armazém de artigos pequenos relacionados com as ferragens, fornecimento industrial, bricolage e construção
Outro fator decisivo que influi na agilidade e no custo das operações é a procura pelo produto ou mercadoria, por isso, os artigos mais requisitados devem estar mais próximos dos cais de entrada e saída das mercadorias. Portanto, nesse sentido, utilizamos o conceito de rotatividade. De acordo com o consumo dos produtos, estes são classificados em:
A. Alta rotatividade: entram e saem continuamente. São muito requisitados.
B. Média rotatividade: entram e saem de forma habitual, mas em menor quantidade do que no caso A.
C. Baixa rotatividade: são as unidades que permanecem por mais tempo no armazém e a sua procura é baixa.
A maioria dos armazéns segue a teoria conhecida como 80/20, ou Diagrama de Pareto, de acordo com a qual, 80% das vendas estão concentradas em 20% dos produtos enquanto os restantes 20% das vendas são distribuídos entre 80% dos restantes produtos.
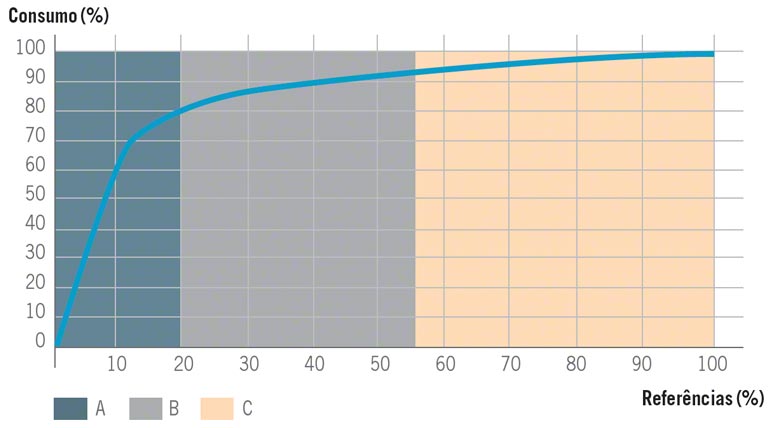
Representação gráfica do Diagrama de Pareto
Como é lógico, o tratamento dado aos fluxos de materiais deverá ser diferente de acordo com a rotatividade, A, B ou C. Aqui são dados dois exemplos de possíveis critérios aplicáveis:
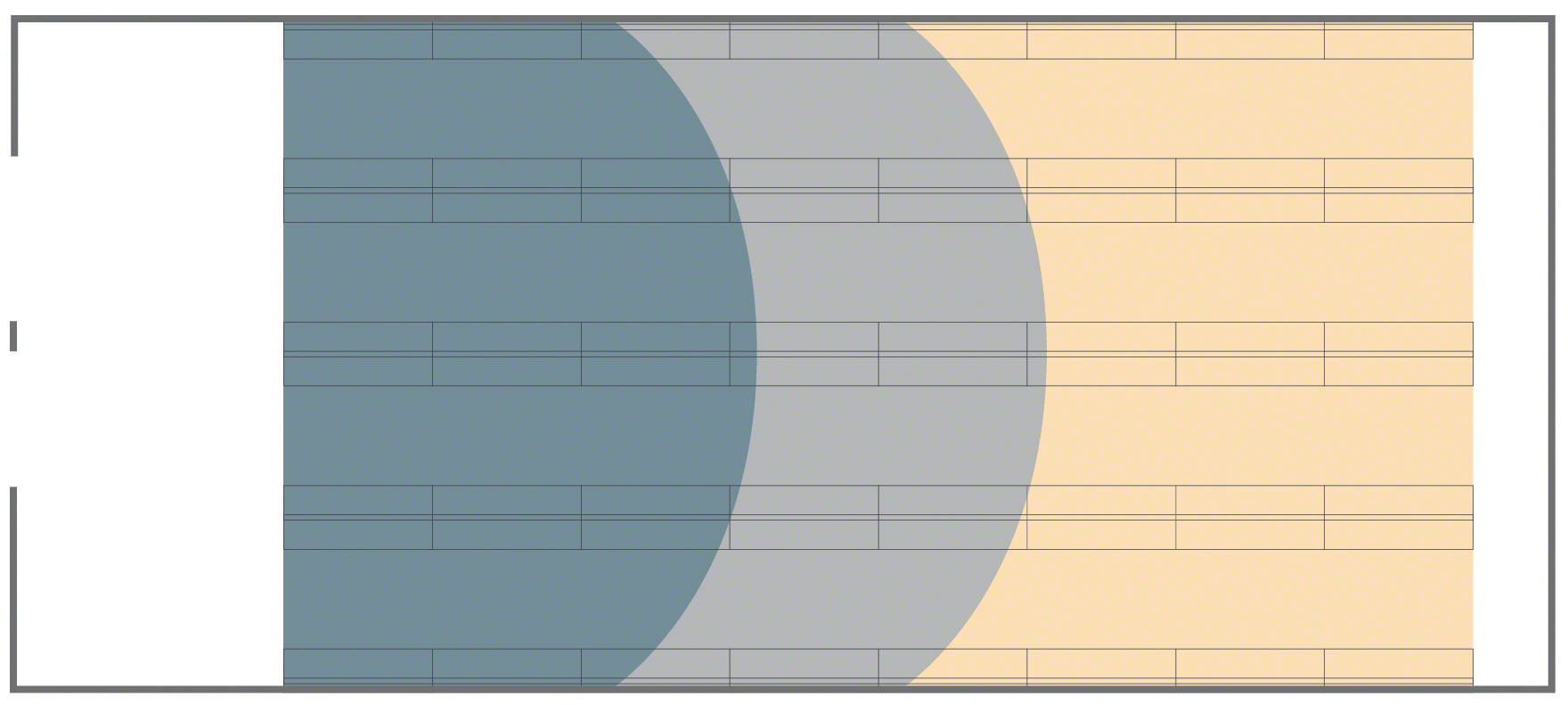
Distribuição de produtos ao longo do armazém em função da sua rotatividade
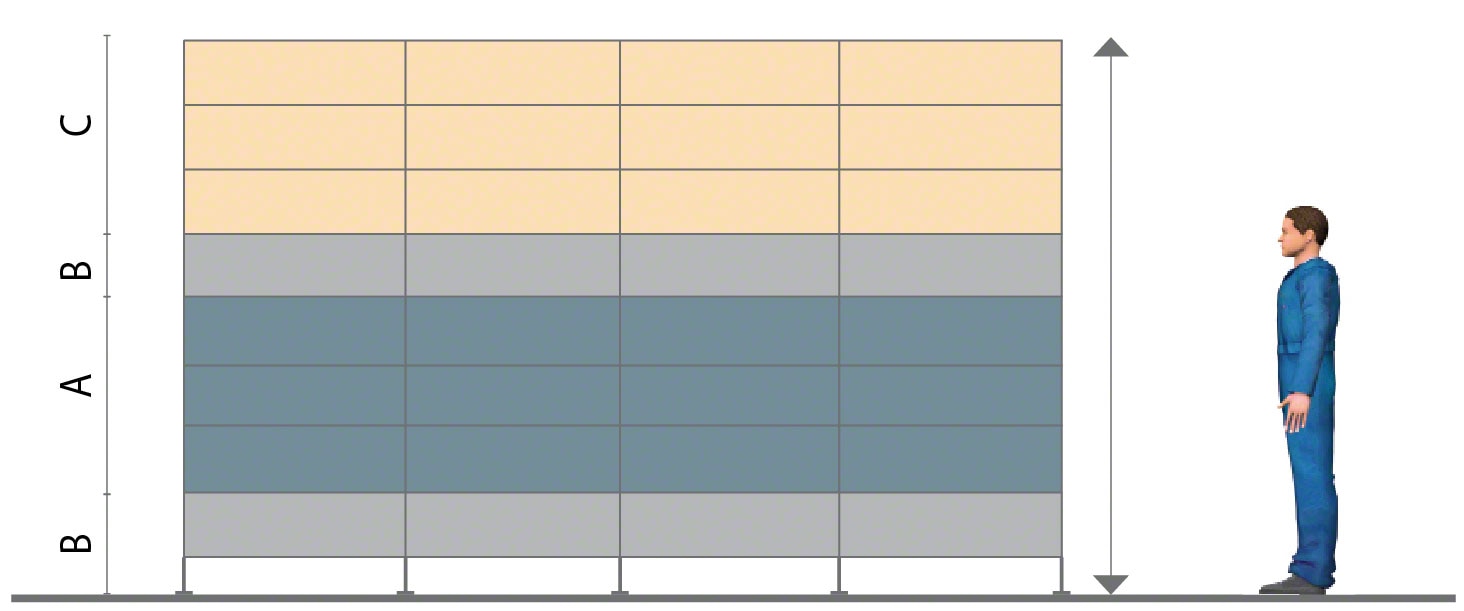
No primeiro exemplo, os produtos A foram posicionados mais perto da zona de receção e expedição. No segundo exemplo, os produtos A foram posicionados na zona mais ergonómica da estante.
Para fazer a distribuição mais lógica de um armazém é necessário analisar cada caso específico, no entanto, pode ser que isso não seja tão simples assim, pois, provavelmente, existem condicionantes que devem ser consideradas.
Por vezes, será mais conveniente colocar os produtos agrupados por sistemas de armazenagem, buscando o maior aproveitamento possível do espaço disponível. No entanto, em outras situações prevalecerá a agilidade e a menor utilização de tempo nas operações. Nos casos em que seja possível, será feita a combinação de ambos os fatores.
Um exemplo que mostra tal facto é a habitual combinação de estantes convencionais e compactas num armazém onde o sistema compacto se destina aos produtos de grande rotatividade.
Algumas conclusões sobre os fluxos e a rotatividade
Os custos de manipulação podem ser reduzidos, portanto, um armazém pode ser mais rentável se distribuir corretamente os produtos de acordo com o seu consumo, se fizer a manipulação adequada, se ordenar corretamente os fluxos e localizar adequadamente os pontos de processos intermédios.
Para termos um armazém otimizado é essencial escolher os equipamentos de armazenagem adequados, tanto o tipo de sistema utilizado como os empilhadores ou os equipamentos de movimentação necessários.
Os diferentes sistemas de armazenagem (convencional, compacto, dinâmico, etc.) apresentam qualidades diferentes que os tornam adequados conforme o caso a ser tratado. Ter um bom Sistema de Gestão de Armazéns (WMS) é fundamental para conseguir os objetivos indicados neste tópico.