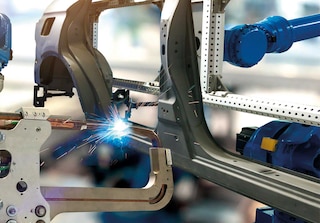
MRP: um marco para o processo de produção
O planeamento MRP (Material Requirements Planning) é um desafio logístico complexo para qualquer instalação. Quanta matéria-prima é preciso? Quando será necessário? Que número de unidades produzir? Essas são algumas das perguntas que os fabricantes vêm respondendo há décadas com a ajuda do sistema de planeamento das necessidades de materiais (MRP).
Neste post vamos analisar tudo o que envolve o planeamento das necessidades de materiais: o que é, como funciona, as suas vantagens e por que foi e é tão importante no processo de produção. Além disso, explicaremos a diferença entre um sistema MRP e um ERP.
O que é um MRP?
O planeamento das necessidades de materiais ou Material Requirements Planning é um sistema projetado para gerir os processos de produção e coordenar antecipadamente as atividades de manufatura, compra e entrega do produto acabado.
O sistema MRP entrou em vigor na década de 1970 e o seu crescimento foi meteórico. Segundo o livro "Production Planning and Control: A Comprehensive Approach", escrito por D.R. Kiran, em 1975, estima-se que 700 empresas já utilizavam o sistema MRP para otimizar os seus processos produtivos. Esse número aumentava 174% ao ano, chegando a 8.000 empresas em 1981, apenas seis anos depois.
Hoje em dia, o sistema MRP é considerado a origem dos atuais programas de computador voltados para a melhoria dos processos industriais: MRP II (Manufacturing Resource Planning), ERP (Enterprise Resource Planning), CRM (Customer Relationship Management), SRM (Supplier Relationship Management) ou MES (Manufacturing Execution System).
O MRP organiza as atividades de manufatura e otimiza a gestão de stock com base nas necessidades da empresa. Com a ajuda do Material Requirements Planning, qualquer fabricante está mais perto de atingir o seu objetivo principal: ter o material exato em todos os momentos para produzir os produtos e entregá-los aos clientes no menor tempo e com o menor custo possível.
Como funciona um MRP?
O sistema MRP requer alguns dados de entrada essenciais:
- Plano mestre de produção: conhecido como MPS (Master Production Schedule), mostra quantos artigos serão produzidos e em que período de tempo.
- Lista de materiais: a BOM (bill of materials) especifica quais matérias-primas, em que quantidade e os processos de produção necessários para obter uma unidade de produto final.
- Registo de stock: detalha as informações relacionadas ao stock (stock disponível, stock a pedido, pedidos cancelados, tempo de espera, etc.). O objetivo é saber qual matéria-prima está disponível para uso imediato.
Com todos esses dados de entrada em mãos, o sistema de planeamento de necessidades de material oferece os seguintes dados de saída:
- Plano mestre de produção recomendado: crie um calendário com datas relacionadas ao processo de produção (início e término), quantidades para cada etapa da rota e a lista de materiais (BOM). Tudo isso procurando atender a procura especificada no plano mestre de produção.
- Cronograma de compras recomendado: mostra as datas em que os materiais comprados serão recebidos, bem como as datas em que os novos pedidos devem ser originados para coincidir com o cronograma de produção.
Desta forma, o sistema MRP garante que receberemos os materiais adequados de forma a manter um nível mínimo de stock para abastecer a produção e, ao mesmo tempo, um planeamento eficiente das atividades de fabricação, compra e entrega do material.
Exemplo de planeamento das necessidades de materiais
Após fazer o plano mestre de produção e a lista de materiais, é determinado que para fabricar um produto final (produto X), são necessárias 2 unidades do material A e 1 unidade do material B. Para cada unidade do material A, 3 unidades da peça C são necessárias e para cada unidade do material B, 2 unidades da peça C e 4 unidades da peça D serão requeridas.
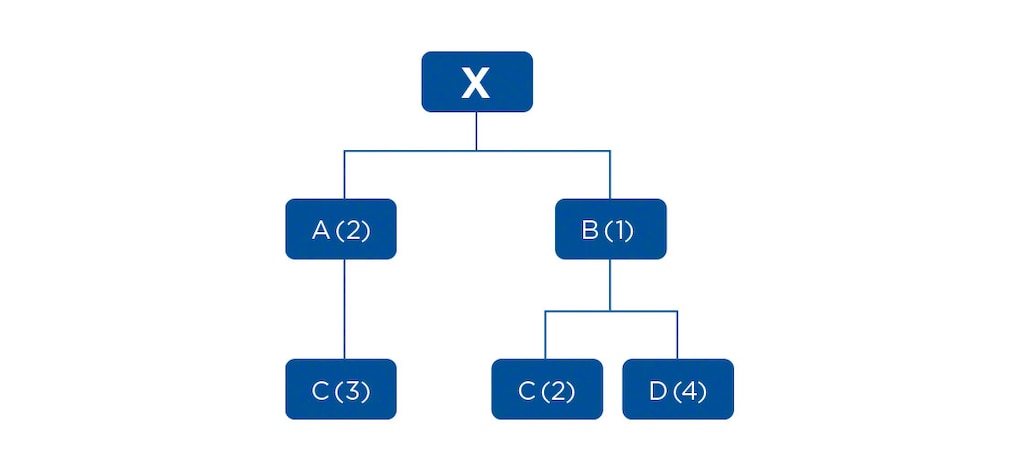
Posteriormente, detalhamos o registo de stock (IRF, Inventory Record File), que reflete o stock disponível e o tempo de espera que leva para receber cada produto:
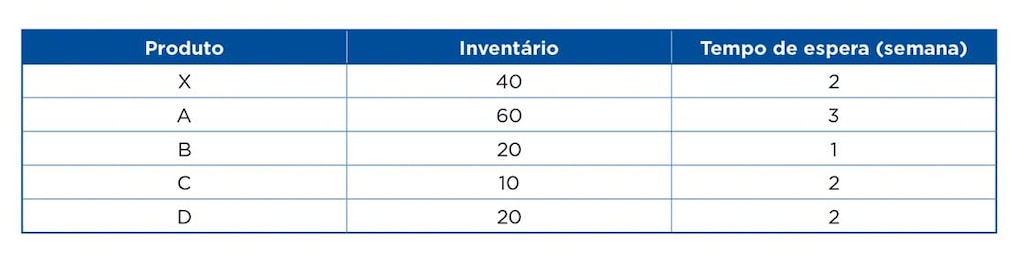
É assim que o planeamento de requisitos de material é resumido na suposição de que temos que produzir 100 unidades do produto X em 10 semanas:
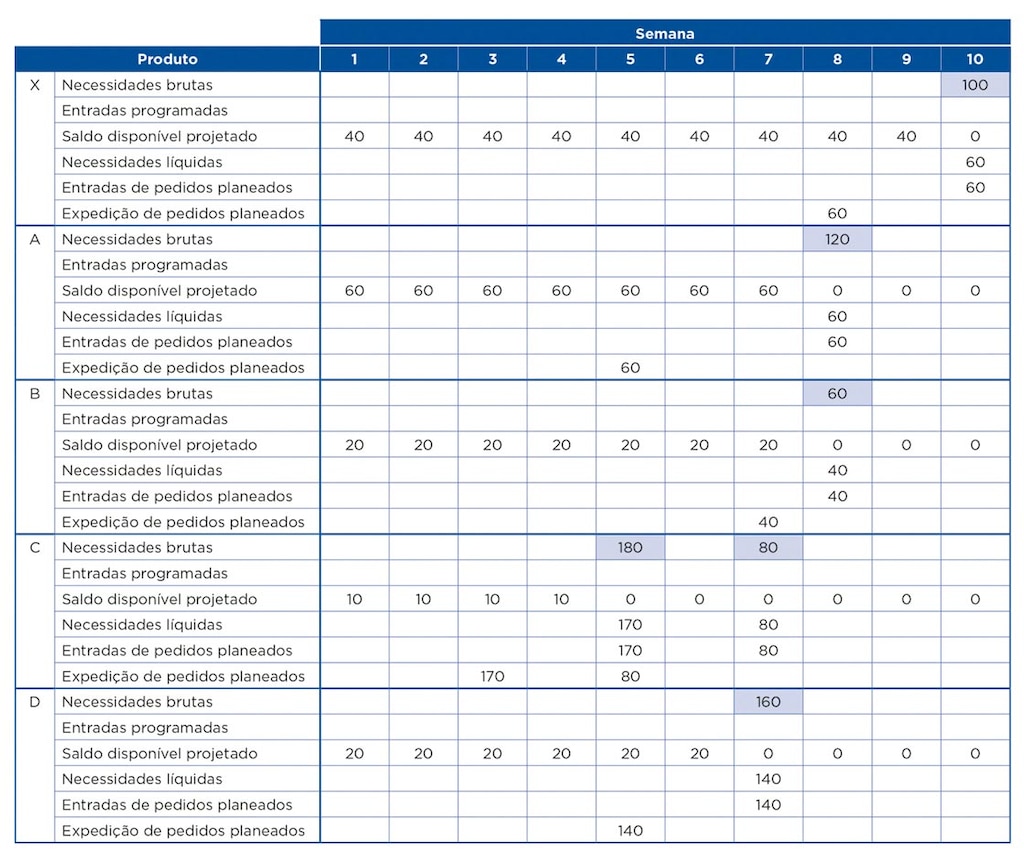
A tabela reflete que, para ter 100 unidades do produto X na semana 10, são necessárias 60 unidades adicionais, além das 40 unidades que já estão disponíveis em stock. Como no registo de stock definimos que o prazo de entrega do produto X é de 2 semanas, o pedido deve ser feito na semana 8.
Se 2 unidades do produto A forem necessárias para cada unidade do produto X, isso significa que, para a semana 8, serão necessárias 120 unidades do produto A. Como já há 60 unidades em stock, a necessidade líquida do produto A também será de 60 unidades. Considerando o tempo de espera, essas unidades deverão ser solicitadas com três semanas de antecedência.
Seguindo o mesmo procedimento, são estabelecidas as necessidades líquidas do produto B, C e D, bem como a semana em que devem ser solicitadas.
Recursos e benefícios de usar um MRP
Dentro de um processo de produção, o planeamento de necessidades de material tem a função de calcular a matéria-prima necessária, os componentes necessários e a quantidade de produto acabado a ser fabricado.
O planeamento das necessidades de materiais oferece os seguintes benefícios:
- Disponibilidade total de matéria-prima para produção.
- Cumprimento de prazos.
- Manter um baixo nível de stock, tanto de matérias-primas quanto de produtos acabados.
- Planeamento das atividades de produção, pedidos de entrega e compras.
- Redução de custos.
O sistema MRP resolve muitos dos problemas que os fabricantes encontram diariamente, especialmente ao comprar matérias-primas. Uma compra incorreta ou insuficiente pode atrasar os prazos de entrega e, no caso de comprar mais material do que o necessário, implica um custo extra de armazenagem.
Diferenças entre MRP e MRP2
No início da década de 80, o sistema MRP (Material Requirements Planning) evoluiu para MRP2 (Manufacturing Resource Planning), um sistema de planeamento mais avançado com um alcance mais amplo. Em termos gerais, as principais diferenças entre os dois sistemas são:
- Além de planear a gestão dos materiais necessários à produção, o MRP2 integra outros departamentos da empresa, como comercial, financeiro, etc.
- Enquanto o MRP trabalha com base no plano mestre de produção, o MRP2 é baseado no estudo da procura e do mercado.
- O MRP2 analisa o comportamento da empresa para executar um planeamento eficiente, enquanto o MRP o faz por meio da prática e da experiência anterior da empresa.
- O MRP é um sistema aberto ao contrário do MRP2, que é fechado. Isso significa que o MRP2 consegue obter feedback dos relatórios que gera, podendo fazer o replaneamento mais alinhado à realidade.
O MRP2 é a versão modernizada do MRP. Além de responder à pergunta quanto e quando produzir, também define quais recursos, em que quantidade e em que tempo serão necessários para realizar a produção.
Diferenças entre MRP e ERP
O sistema ERP (Enterprise Resource Planning) foi usado pela primeira vez na década de 1990 e é ainda mais completo e versátil do que os seus sistemas anteriores de MRP. Se há algo que o caracteriza e o torna diferente do MRP é porque tem a capacidade de centralizar no mesmo sistema todas as áreas da empresa.
Em outras palavras, MRP é um software que funciona sozinho, enquanto o ERP integra e combina os sistemas computacionais usados por cada departamento para criar um banco de dados centralizado. Desta forma, qualquer área da empresa pode aceder informações em tempo real, controlar os fluxos de trabalho, minimizar erros e comunicar com outras áreas.
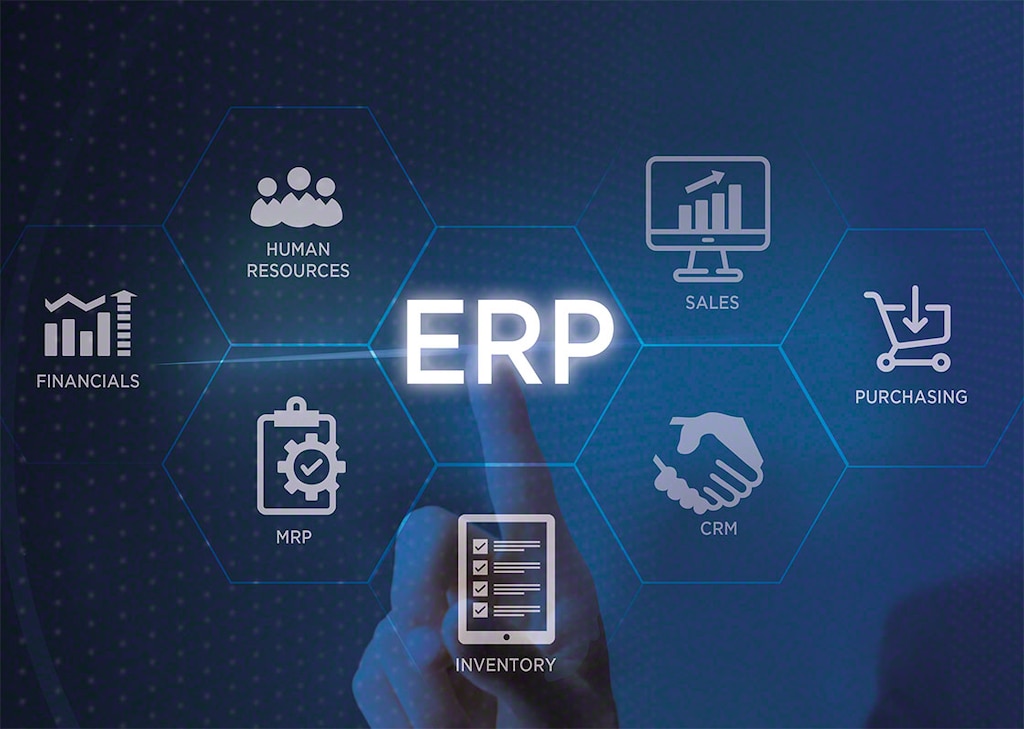
MRP: na esteira dos avanços tecnológicos
Após cinquenta anos de atuação, é justo afirmar que o planeamento das necessidades de materiais marcou um antes e um depois no processo produtivo. A sua essência, que não é outra senão antecipar as necessidades para poder planear, foi adaptada às novas tecnologias com o objetivo de aumentar a rentabilidade da cadeia de abastecimento.
Na Mecalux, apostamos sempre nas soluções tecnológicas mais inovadoras do mercado, tanto para a gestão da armazenagem como da logística, como é o caso do Easy WMS. Este sistema pode ser integrado a qualquer ERP para que ambos os sistemas transfiram dados e informações destinadas a obter maior produtividade no armazém.
Entre em contato connosco se quiser uma equipa de especialistas para ajudá-lo a obter o máximo da sua cadeia de abastecimento.