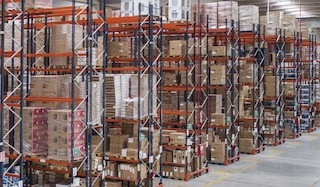
Os 10 problemas logísticos mais comuns num armazém
A contínua evolução em direção aos mercados digitais e as novas exigências dos clientes levou a um aumento significativo dos problemas logísticos, especialmente daqueles relacionados à gestão do armazém.
Mas, quais são os problemas logísticos mais comuns? Identificamos os dez mais habituais que ocorrem num armazém e sugerimos algumas soluções para minimizar suas consequências.
1. Espaço mal aproveitado
A falta de espaço de armazenamento é um dos principais problemas que a maioria das empresas enfrenta. Diante desta situação, causada principalmente pelo aumento da atividade, as empresas têm a obrigação de otimizar o espaço se não quiserem fazer um considerável desembolso económico em solo logístico.
Uma das soluções mais frequentes para maximizar o espaço sem alterar a superfície é aproveitar a altura do armazém mediante a utilização de estantes de maior altura ou plataformas e passarelas. Também podemos otimizar a superfície instalando sistemas de armazenagem compactos, como o Pallet Shuttle, estantes móveis Movirack ou estantes compactas drive-in.
2. Falta de organização da mercadoria
A falta de organização da mercadoria ocasiona erros e atrasos no momento de procurar um determinado produto, dificultando o cumprimento dos tempos de entrega. Um armazém organizado é o primeiro passo para a eficiência logística.
Para evitá-lo, é preciso elaborar uma estratégia eficiente de localização da mercadoria que tenha em consideração as características das referências, os sistemas de armazenagem disponíveis, a rotatividade da mercadoria e as deslocações dos operadores.
A utilização de um sistema de gestão de armazéns garante o controle integral do estoque existente no armazém ao sincronizar as ordens de entrada e saída. Um SGA, por exemplo, automatiza o processo de localização das referências no armazém (slotting) mediante critérios e regras previamente configurados.
3. Erros no picking
Desde recolher o artigo errado até misturar vários pedidos numa única ordem, o custo da logística reversa ─ a devolução de artigos ─, causada por falhas no picking, tem graves consequências na logística de uma empresa.
Os erros no picking representam um elevado custo para o negócio. De acordo com certos estudos, o seu impacto médio estimado situa-se em cerca de 17 € por pedido.
Numa operação tão complexa como o processamento de pedidos, onde habitualmente os operadores elaboram vários pedidos de diferentes referências, automatizar é a solução para eliminar a taxa de erros e aumentar o número de picks por hora que são completados no armazém.
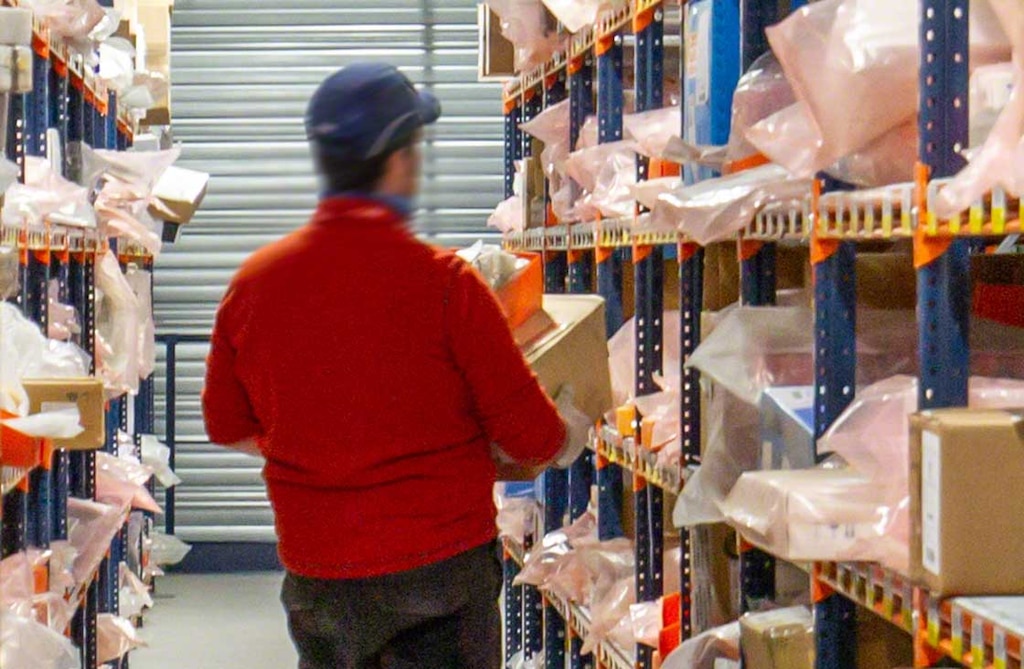
4. Falta de rastreabilidade
Num contexto de cadeia de abastecimento integrada, clientes e fornecedores desejam saber em detalhes as matérias-primas que foram utilizadas para a elaboração do artigo e os processos produtivos e logísticos pelos quais passou até chegar às suas mãos.
A rastreabilidade do produto, o atributo logístico que permite registar e identificar cada produto desde sua origem até ao seu destino final, é especialmente delicada em setores como o farmacêutico ou o agroalimentar. Um erro de rastreabilidade pode causar graves problemas para os clientes que adquiram o produto, assim como para a empresa fornecedora.
A implementação de um software logístico como um SGA garante a rastreabilidade do produto desde a sua entrada no armazém até à sua expedição. Além dessa aplicação, existem outros softwares no mercado que reforçam esse atributo logístico, tal como a funcionalidade avançada do Easy WMS, o sistema SGA para produção. Esse módulo sincroniza o pulmão de abastecimento com o de produção permitindo monitorar o processo de produção em um armazém.
5. Inventário desatualizado
Conhecer e planificar o stock de um armazém é indispensável para manter a produtividade em todas as operações logísticas. Por isso, um armazém com um inventário desatualizado pode trazer graves consequências para uma empresa, desde erros na localização de produtos até uma possível rutura de stock.
À medida que as empresas crescem e incorporam mais referências em seu armazém, a implantação de um Sistema de Gestão de Armazém se converte em uma ferramenta necessária para estar permanentemente ciente do stock existente no armazém.
6. Erros na manipulação da mercadoria
Manipular corretamente as unidades de carga para formar os pedidos é um dos elementos-chave para reduzir erros e aumentar a produtividade. É necessário garantir que os operadores estejam convenientemente formados, que o armazém tenha os equipamentos de movimentação adequados e que estes passem pela manutenção necessária.
No entanto, a opção que melhor garante a manipulação adequada da mercadoria é a automação dos sistemas de armazenagem. Os responsáveis por gerir a logística optam por substituir os equipamentos de movimentação convencionais, como porta paletes e empilhadores contrabalançados, por transportadores e transelevadores, com o objetivo de agilizar a circulação da mercadoria entre os diferentes processos logísticos.
Além disso, ao manusear a mercadoria, é importante garantir a estabilidade das unidades de carga, habitualmente paletes ou caixas, para assegurar a estabilidade do volume ao longo de todas as operações realizadas no armazém.
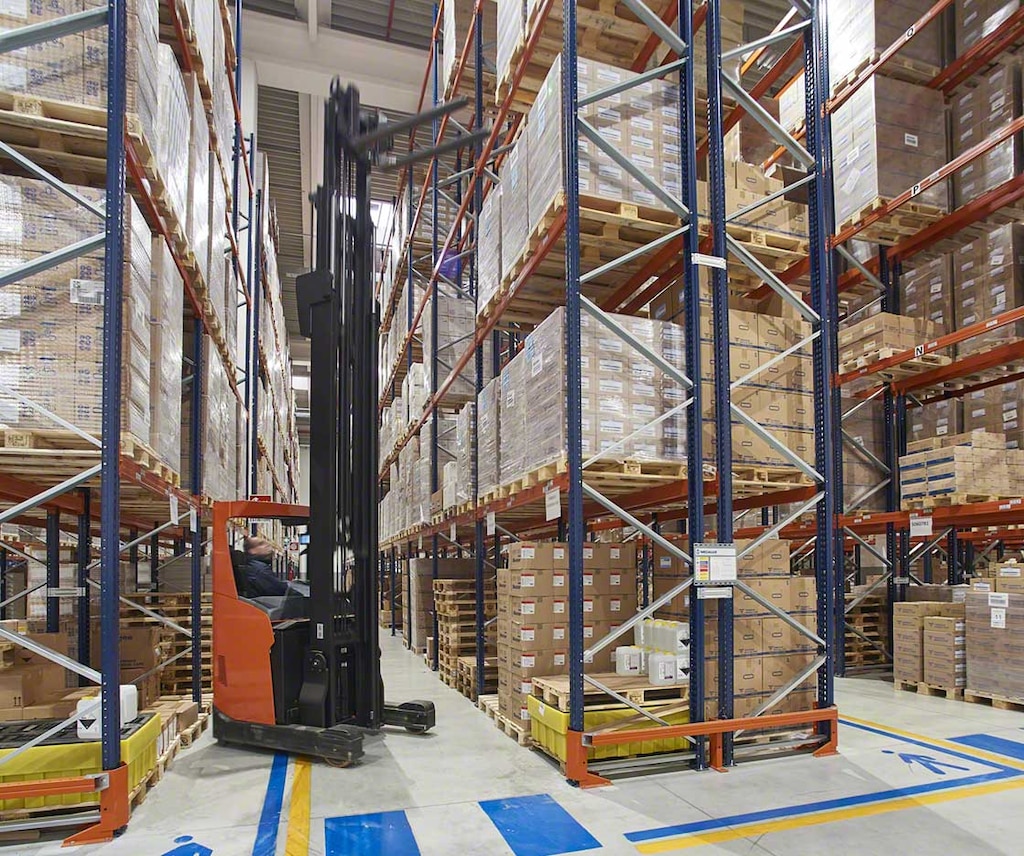
7. Atrasos na expedição
A expedição da mercadoria é o último processo pelo qual passa um produto antes de ser expedido, seja para o cliente final ou para outro centro de distribuição ou produção.
Para que esse processo seja completado com sucesso é aconselhável planificar as entregas a realizar, consolidar a mercadoria de forma eficiente, verificar toda a documentação necessária para a expedição correta e carregar a mercadoria no camião de forma rápida e segura.
Um Sistema de Gestão de Armazém é capaz de agrupar os pedidos por rota de distribuição, tipo de veículo, cliente ou prioridade do envio, entre outros.
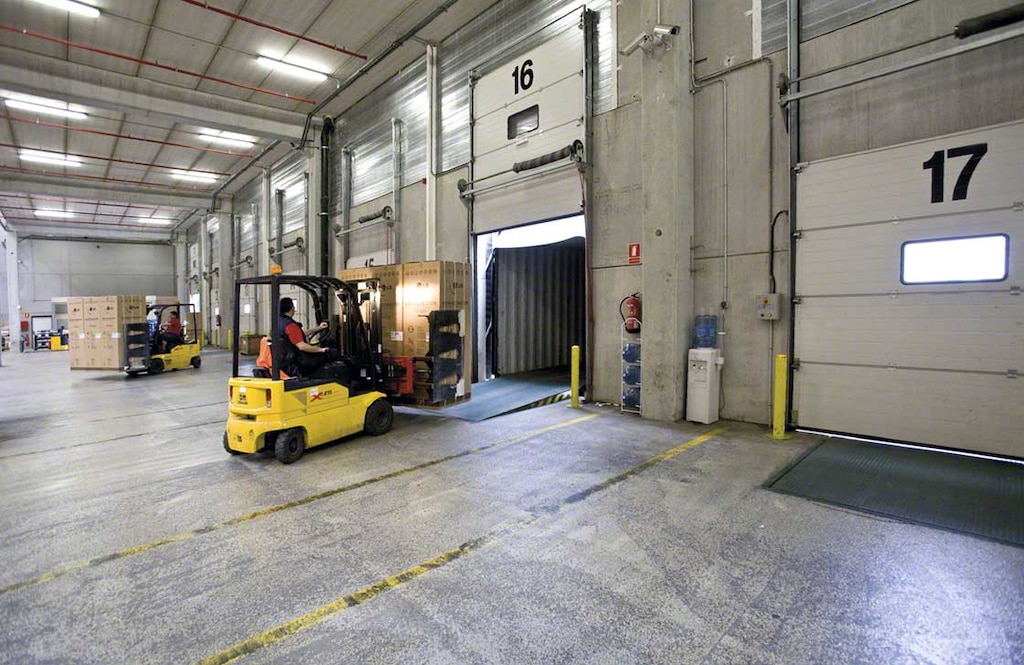
8. Sinalização deficiente do armazém
Num espaço onde convivem operadores, mercadoria e equipamentos de movimentação, é obrigatório sinalizar o armazém para minimizar os riscos de acidente. Os sinais devem estar perfeitamente localizados e visualmente diferenciados no piso e nas estantes para seguirem as medidas de segurança. Tais sinais podem ser de diferentes cores, símbolos e formas dependendo das suas características e da mensagem que devem transmitir.
A norma que obriga e regula a sinalização do armazém está sujeita à Diretiva 92/58/CEE do Conselho Europeu, que define como devem ser os sinais num armazém. Esses sinais podem ser de diferentes cores, símbolos e formas, dependendo das suas características e da mensagem que devem transmitir.
9. KPIs logísticos incorretos
A melhor ferramenta para realizar ações de melhoria contínua no nosso armazém é através dos indicadores de desempenho ou KPIs logísticos (Key Performance Indicators). Através dos dados e da comparação com o histórico da empresa, podemos monitorar o desempenho de uma operação para identificar oportunidades de melhora.
Os KPIs logísticos permitem medir todas as operações efetuadas num armazém: recebimento de mercadorias, armazenamento, preparação de pedidos, gestão de inventários, expedições, entregas, transporte e gestão de devoluções, entre outras. Se não utilizarmos corretamente esses indicadores ou concentrarmos os nossos esforços em analisar KPIs incorretos, será muito complicado identificar evoluções positivas ou negativas e agir de acordo para atingir a excelência logística.
Um módulo como o Supply Chain Analytics Software monitora toda a atividade que ocorre no armazém, calculando os KPIs logísticos mais relevantes para a sua posterior análise.
10. Integração com outros departamentos (ERP)
O chefe de armazém deve de se coordenar com os demais departamentos da empresa para conseguir o objetivo final de toda a logística: o pedido deve chegar no prazo e na forma estabelecidos com o cliente.
Para tal finalidade, os diferentes softwares logísticos se integram dentro do ERP (Enterprise Resourcing Planning), um programa informático que agrupa todas ou a maioria das divisões de uma empresa, tais como contabilidade, marketing, departamento comercial, etc.
Uma coordenação inadequada entre o armazém e a divisão de vendas pode ocasionar erros nos pedidos ou pedidos incompletos, o que representa graves consequências económicas para a empresa.
Beneficie de um armazém mais eficiente
Em linhas gerais, a automação, tanto da operação quanto da gestão de um armazém mediante um SGA, é a melhor estratégia para um armazém livre de erros e muito mais eficiente.
Se o seu armazém tiver algum dos problemas citados anteriormente ou acredita que chegou a hora de robotizar tanto o armazenamento quanto a gestão de seu centro de distribuição, não hesite em entrar em contato com a Mecalux. Uma equipa de especialistas vai ajudá-lo a resolver qualquer contratempo para que aproveite ao máximo os seus processos logísticos.